Posts selected fromManagement Blog - Engineering Blog - Investing Blog and other blogs - Using Scientific Knowledge to Drive Policies that Create a Better World
We can’t afford to elect people that don’t have an understanding of how to make wise decisions or how to ensure scientific knowledge forms the basis of policy when it should, such as: overfishing, pollution, global warming, the health care benefits vaccines provide when they are used properly, the dangers of abusing antibiotics, etc..
We need to elect leaders like those that took the steps to have the EPA clean up the incredibly polluted USA. We need to elect leaders that put the policies in place to reduce the overfishing in our waters. We need to elect leaders that care about our country and will learn what they need to from those that know the science. continue reading: Using Scientific Knowledge to Drive Policies that Create a Better World - Jobs to be Done
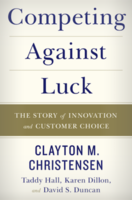 If you see your job from the customer’s perspective you may change the scope of your offerings. You can add services that help the potential customer chose you. In the book, they explore the example mentioned in the article in more detail. They also discuss how an online university changed their processes to address the issues their potential customers faced in the “hiring” process. They changed, not the “product” (education), but the processes supporting potential students making the decision to hire Southern New Hampshire University. continue reading: Jobs to be Done - Toyota as Homebuilder
many organizations don’t apply many concepts that have been proven effective for decades. So I hope Toyota gets into any business that continues to provide lousy value to the consumer (at least those where that consumer is me). I wish they would create their own credit card (they offer Toyota branded Visa and MasterCard credit cards now, in Japan), provide high speed internet service and run an airline.
Toyota is probably too smart to try and run an airline in the US (only Southwest seems to be able to that profitably).
...
On the Toyota web site they list the following areas of non-automotive Toyota business: financial services, information and communications, marine and most surprisingly Biotechnology and Afforestation. Toyota states: “Biotechnology may seem far removed from the auto industry. It is, however, closely related to automaking in the context that they are both aiming to achieve a sustainable society, and their close relationship can be seen in the new Raum, launched in May 2003, which uses parts made from bioplastics.” continue reading: Toyota as Homebuilder - Why Do People Fail to Adopt Better Management Methods?
It is confusing to know that better methods exist but to see those better methods being ignored. It seems that if there were better ways to manage, people would adopt those methods. But this just isn't the case; sometimes better methods will be adopted but often they won't. People can be very attached to the way things have always been done. Or they can just be uncomfortable with the prospect of trying something new. continue reading: Why Do People Fail to Adopt Better Management Methods? - Robots for Health Care from Toyota
Most often innovation efforts take the form of understanding the jobs your customers are using your products and service for now and developing new solutions to delight those customers. This is difficult for companies to pull of successfully.
Occasionally innovation involves meeting completely new needs of customers. For example Toyota started as a loom company and is now known as a car company. Making such a radical change is not often successful.
Will Toyota be able to add robots to the products it produces successfully? I believe they have a chance. But it won’t be easy. continue reading: Robots for Health Care from Toyota - Creating a Deep Commitment to Delighting Customers
Those organizations that can delight customers today and take the steps today that position the organization to delight customers in the future will prosper and grow. But building and maintaining a management culture that reinforces delighting customers and long term thinking is quite difficult.
...
Successfully delighting customers requires much more than a wish that customers were delighted with our organization. It requires knowing what your customers want and creating system that can reliably delivering that to customers.
continue reading: Creating a Deep Commitment to Delighting Customers - The Quick Fix
W. Edwards Deming
One trouble with American industry today is that top management supposes that one lecture or one day will do it. “Come, spend a day with us, and do for us what you did for Japan, that we too may be saved.”
continue reading: The Quick Fix - Technological Innovation and Management
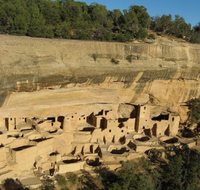 Organizations need to be designed to be robust and to cope well with the increasingly rapid pace of transformative innovation. This again reinforces the importance of management improvement practices that I have been writing about here (on the Curious Cat Management Improvement blog) for more than 10 years. Organizations that do not delight customers, know the jobs to be done that their customers have, focus on the future (long term thinking), understand how to use data, have well designed processes that allow those at the gemba to know what to do and know how to rapidly adjust based on new realities and possibilities are at great risk. continue reading: Technological Innovation and Management - Agile Software Development and Deming's Ideas
- The Importance of Critical Thinking and Challenging Assumptions
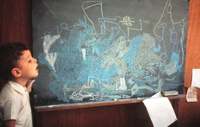 Critical thinking is important to applying management improvement methods effectively. It is important to know when decisions are based on evidence and when decisions are not based on evidence. It can be fine to base some decisions on principles that are not subject to rational criticism. But it is important to understand the thought process that is taken to make each decision. If we are not clear on the basis (evidence or opinion regardless of evidence) we cannot be as effective in targeting our efforts to evaluate the results and continually improve the processes in our organizations.
...
Changing the culture to one that values understanding and learning takes time. That process must be done with an understanding of psychology and the challenges of getting people to evaluate decisions. Creating a culture where it is expected that people think about the evidence and are comfortable explaining and defending the reasoning behind decisions is extremely important. continue reading: The Importance of Critical Thinking and Challenging Assumptions - Management Improvement History
I do believe we need to improve our practice of Quality (and to do that we need to understand what happened in the past and why it was not more successful). The idea that Design of Experiments (DoE) was at the core of some Quality Movement to me is not at all accurate.
In my experience only a few Quality professionals today understand what it means and how it should be applied. The idea that it was common place in the 40’s I seriously doubt (though I don’t have first hand knowledge of this). I find it difficult to believe we would have decided to stop using DoE if it was commonly done previously. The understanding I have from those that should know (like George Box and previously my father – Bill Hunter) is that it was not at all common practice and still is not outside of a few industries and even there it is isolated in the domain of a few experts.I do have first hand knowledge of the 80’s and the idea that we did “employee training in problem solving, team activities and just-in-time inventory” well is not even close to accurate. We sent people to training on these things but other than JIT inventory the effectiveness of these efforts were poor (with a few exceptions that really did well).
“Quality” is not being practiced anywhere close to the level with which I am satisfied with in more than a few organizations. We have huge improvements to make in the practice of DoE, SPC, process improvement, having decisions made by the appropriate level (as close to the issue as possible), leadership, teamwork, data based decision making, the use of basically all the Quality tools, systems thinking, transformation… continue reading: Management Improvement History - Taguchi Loss Function
In practice, I have seen the concept of the Taguchi Loss Function used quite a bit. I have never actually seen any losses quantified and totaled and shown on a graph. I think focusing specifically on who suffers a loss and what that loss could be, can help. I think actually quantifying the losses to society can be daunting. So, while I see the value in framing the concept that way I think to actually get the losses quantified you are best served by starting with those closest to the process and then adding additional loses to those results.
Second, if you attempt to use the concept to help you manage (as a guide in decision making) the impacts to society are a factor, but, I think the loss to your company, the customer and perhaps the end user are most important. A negative impact to society at large is not going to have the same impact to a decision maker as the same negative impact to the customer. The decision maker will likely be willing to invest more to reduce the loss to a customer than to society at large (and that seems logical and sensible to me). continue reading: Taguchi Loss Function - Operational Excellence
Saying the organization is focuses on new principles (partnering, lean, etc.) is not the same as applying those principles with the great success that Toyota does. That difference is huge and is driving many companies to outsource and try to dramatically cut costs. Reducing costs should be the outcome of improving efficiency.
Toyota is successful manufacturing in the USA.
...
I would agree that many companies don’t understand the critical importance of management excellence. Rather than take the difficult path to lead real change in their organization they focus on simple cost cutting measures (though usually not cutting executive salaries which have grown dramatically and are excessive in the USA compared to the rest of the world). That won’t work. continue reading: Operational Excellence - Lean Management in Policing
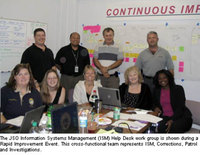
Hiring of school crossing guards made more expedient. “This one’s amazing,” Sheriff Rutherford chuckles. “It was taking us 68 days to hire someone from our eligibility list because we were sending candidates all over for different parts of the interview process. Now it takes us just three days to make a decision because we’re practicing ‘one-stop hiring.'”
continue reading: Lean Management in Policing - Targets Distorting the System
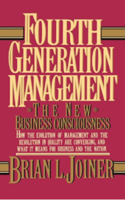 I still remember Dr. Brian Joiner speaking about process improvement and the role of data well over a decade ago. He spoke of 3 ways to improve the figures: distort the data, distort the system and improve the system. Improving the system is the most difficult. continue reading: Targets Distorting the System
|