Posts selected fromManagement Blog - Engineering Blog - Investing Blog and other blogs - People: Team Members or Costs
Both Toyota and GM seek to use technology to improve but Toyota sees the technology as useful to help people to be more efficient, eliminate menial repetitive tasks, eliminate tasks that cause injury… and it seems to me GM saw technology as a way to eliminate people. The action showed a company that viewed people as a cost to be eliminated. GM did not act as though people were their “most important assets” as we so often hear, but see so little evidence of in the action of companies.
Toyota does try to reduce overall costs (including labor costs) by continually improving and making cars more and more efficiently (so they can produce cars using fewer hours of labor in the future than they need today). Trying to become more efficient by engaging everyone in the effort is a part of the system of management at Toyota. The current Toyota employees are an important part of the system and are not viewed as a cost to eliminate.
continue reading: People: Team Members or Costs - Dell Falls Short
Don’t give management a free pass just because they cave in to short term thinking. Management should know better and has a responsibility to do better. It is predictable that if management fails to setup an effective management system that they will fall victim to short term thinking. Still that doesn’t mean they are not responsible for making decisions. They are the managers of the company not some analyst on Wall Street. continue reading: Dell Falls Short - Brainstorming Under Attack
Brainstorming is about creating an opportunity to bring new ideas the forefront.
There are other useful tools such as the affinity diagram which can serve as another option (or can serve as a tool to work with the results of brainstorming).
And Edward DeBono has excellent creativity tools, like his 6 thinking hats. Brainstorming is a useful tool when applied properly but it is only one tool and other tools should be used also. continue reading: Brainstorming Under Attack - Lean National Health System
This is an example of focusing on improving the system which will then result in improved measures (cost savings for example). This systems approach contrasts with cutting costs by cutting every budget by 5% across the board which often fails. Without improvements in the system reducing budgets just reduces capability. continue reading: Lean National Health System - Problems Caused by Performance Appraisal
People are increasingly challenging the notion that we just have to live with performance appraisal systems. As usually, I will make my suggestion that chapter 9 of the Leader’s Handbook offers great material on performing without appraisal (and the rest of the book is great too). continue reading: Problems Caused by Performance Appraisal - Better and Different
The answer, as I see it, is to be better and different (when necessary).
...
if you have to choose one, just being better will work most of the time. The problem is (using an example from Deming, page 9 New Economics) when, for example, carburetors are eliminated by innovation (fuel injectors) no matter how well you make them you are out of business.
Often people mistake Deming’s ideas as only about being better. He stressed not only continual improvement (Kaizen, incremental improvement, SPC) but also innovation. He stressed innovation both in the normal sense of innovating new products for customers and also innovation in managing the organization. continue reading: Better and Different - Brainstorming Under Attack
Brainstorming is about creating an opportunity to bring new ideas the forefront.
There are other useful tools such as the affinity diagram which can serve as another option (or can serve as a tool to work with the results of brainstorming).
And Edward DeBono has excellent creativity tools, like his 6 thinking hats. Brainstorming is a useful tool when applied properly but it is only one tool and other tools should be used also. continue reading: Brainstorming Under Attack - Lean Beyond the Factory Floor
Experts (in TQM, Deming’s idea’s, Six Sigma, BPR, Lean…) always stress the importance of involving not just others (when talking to management) but their (managers) work too. But fairly consistently management adopts improvement ideas mostly for others, not for their own work. As organizations apply management improvement ideas on some portion of the work the talk of going beyond “factory floor” improvements becomes more common as improvements are seen where it is applied.
Fast Cycle Change in Knowledge-Based Organizations by Ian Hau and Ford Calhoun, Jun 1997 is a good example of lean thinking, eliminating waste… outside the factory floor. continue reading: Lean Beyond the Factory Floor - Kleptocrat CEOs and Their Apologists
CEOs, and their cronies, were well paid decades ago. As their greed about their pay got to be unethical Peter Drucker started to speak out against their ethical failures. As those abuses became more extreme he increased his objections.
...
I want a CEO that is paid well and seeks their reward not by taking from the corporate treasury but by providing great jobs, customer happiness and an improved society. continue reading: Kleptocrat CEOs and Their Apologists - Management Advice Failures
I share this frustration with declaring old ideas new: Management Improvement, Better and Different, Quality, SPC and Your Career, Deming and Six Sigma, Management Lessons from Terry Ryan, Everybody Wants It, Toyota’s Got It, Fashion-Incubator on Deming’s Ideas and on and on.
Why does this matter? Two reasons, most importantly to me is that when we fail to value the best ideas, instead valuing the new ideas, we are not as effective as we could be. We often accept pale copies of good old ideas instead of going to the good old ideas – which will often lead to a much richer source of knowledge. When I compare copyrighted versions of management thinking to ideas from people like Ackoff, Deming, Ohno, Scholtes, McGreggor the depth and richness of those I admire is much greater than the packaged solutions as I see it (and they are often more concerned with furthering the practice of management than further their brand). Second, it is often dishonest, or at least sloppy thinkers, that don’t acknowledge the history of management ideas. continue reading: Management Advice Failures - More on Obscene CEO Pay
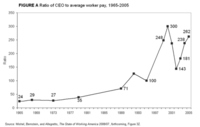 Unfortunately this reverse robin hood (steal from the workers, stock holder, customers…) and give to the CEO tale continues. Hopefully someday soon we can at least turn the momentum in the right direction (stopping these incredibly excessive “pay” packages). Even then it will take quite a deal of reducing these ridiculous “pay” packages to reach some sense of decency. continue reading: More on Obscene CEO Pay - Understanding Psychology: Slogans – Risky Tools
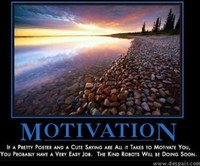 Slogans mainly are bad. But like most things they can be used in ways that help or hurt. The main problem is when they substitute for a method to achieve the aim (most of the time). If the slogan serves like a mission statement to focus people on something useful to focus on and it is one minor part of a system to achieve a result it can be fine and even useful. continue reading: Understanding Psychology: Slogans – Risky Tools - Employee Ownership
I have always liked the idea of employee ownership. To me this can be a great help in creating a system where employees, owners, customers, suppliers work together. Alone an Employee Stock Ownership Plan (ESOP) does little. But as part of a system of management it is something I think can be beneficial. continue reading: Employee Ownership - Is Innovation Needed to Keep Manufacturing in the USA?
There is no ace in the hole. If countries want to keep manufacturing jobs they are going to have to do lots of things right. No country has such an advantage they can expect to rely on their country being more innovative (or offering cheaper labor, or their citizens working harder or…) than all the other countries in the world.
Innovation has been an advatage for the USA. It should continue to be an advantage for the USA but many other countries will innovate very well (Japan, Germany, China, Korea, Singapore, England…). The USA has many assets: transportation infrastructure, banking, rule of law, educated and skilled workforce, huge market, decent tax laws, engineering education… The key will be to keep focusing on the whole system (and fix things like huge budget deficient, huge current account deficit, excessive health care costs, excessive executive pay…).
I also believe a key competitive advantage will be in applying management improvement concepts such as lean manufacturing. continue reading: Is Innovation Needed to Keep Manufacturing in the USA? - Trust: Respect for People
Management then vowed that this (layoffs in 1950) would be the first and last time such an event would come to pass at Toyota, and, in a gesture of respect to former employees, Kiichiro resigned from his position as president of the company.
A bit different than laying off tens of thousands of workers and then taking huge bonuses [the broken link was removed]. And in case you don’t know, I think Toyota’s approach is more honorable and what should be aimed for (I wouldn’t say the president always should resign but it should be a significant admission of failure).
Does this mean no workers ever come into conflict with Toyota management? No. But Toyota’s respect for workers is qualitatively different than that of most companies.
Related: Bad Management Results in Layoffs continue reading: Trust: Respect for People
|