Blog posts on lean managementPosts selected fromManagement Blog - Engineering Blog - Investing Blog and other blogs - Toyota Engineers a New Plant: the Living Kind
Toyota’s vision:
First, making things that benefit both people and the world as a whole. … Second, as a member of society, we must fulfill our responsibilities to all stakeholders. We must provide to customers cleaner, safer, and more attractive products with excellent value. To shareholders, we must enhance share value through long-term and stable growth by increasing profits and paying appropriate dividends. With business partners, we must engage in fair business based on a spirit of mutual benefit.
To our employees, we must provide a workplace where they can work with pride based on mutual trust and responsibility between labor and management, and respect for people.
continue reading: Toyota Engineers a New Plant: the Living Kind - Marketing in a Lean Company
- Eliminating Complexity from Work
as much as half of the activities of about sixty people had been to set up and take down jobs, expedite, move material, count material, and do other tasks that were unnecessary in the new process.
Tim Fuller's article discusses how much inneficiency was removed from the process by adopting single piece flow in 1985. How long did it take for management practice to understand this? Certainly this understanding wasn't widespred in 2005. I am not even sure it if it is widely understood and systems have been designed or redesigned with this knowledge in 2017. continue reading: Eliminating Complexity from Work - Going Beyond (or away from) Lean Thinking?
“Lean,” as it is commonly implemented, is not enough.
I believe ideas from Deming that are missing from many lean efforts would be helpful (Toyota applies Deming’s ideas to a much greater extent than those modifying Toyota’s practices for their organization).
Mainly what is needed is for organizaitons to more deeply impliment lean thinking. There is not a need to "go beyond" lean - the problem is poor implimentation not good implimentation of a management philosophy that has been overtaken by some new management ideas that were missing. continue reading: Going Beyond (or away from) Lean Thinking? - Be Thankful for Lean Thinking
Through better information engineering, supply chain improvements have resulted in a reduced bullwhip effect, lower inventory levels, reduced logistics costs, and streamlined payments. These improvements appear to have helped produce macroeconomic benefits such as more stable economic output and higher productivity growth.
continue reading: Be Thankful for Lean Thinking - Interview with Jim Womack (2005)
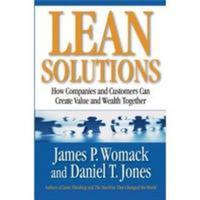
The whole idea of lean solutions is to start with today’s customer in today’s circumstances and ask what the customer really wants. When we do this, the first thing to note is that manufactured goods have gotten vastly better, somewhat cheaper
...
But we have also noticed for years the growing gap between the factory, where things are getting better, and the situation of providers and consumers where it often appears that things are getting worse.
continue reading: Interview with Jim Womack (2005) - Toyota Special Report: Thinking Production System
Minoura warns “simply introducing kanban cards or andon boards doesn’t mean you’ve implemented the Toyota Production System, for they remain nothing more than mere tools. The new information technologies are no exception, and they should also be applied and implemented as tools.”
Early in his career, Minoura worked under Taiichi Ohno, recognized as the creator of the Toyota Production System. Ohno, through tireless trial and error, managed to put into practice a “pull” system that stopped the factory producing unnecessary items. But Minoura observes that it was only by developing this “loose collection of techniques” into a fully-fledged system, dubbed the Toyota Production System or TPS, that they were able to deploy this throughout the company continue reading: Toyota Special Report: Thinking Production System - Not Lean Retailing
Nothing is wrong with major decisions being made by the leaders but the article leaves the impression many non-major decisions are cetralized too. That is a problem for those who believe in management improvement ideas including lean thinking.
...
Again moving away from good lean management ideas such as: longevity of management, focus on value of employees rather than cost of employees… continue reading: Not Lean Retailing - Deming and Toyota
I believe Toyota applied Deming’s ideas to create a management system and continued to develop that system to create the Toyota Production System (also known as lean manufacturing). continue reading: Deming and Toyota - PBS Documentary: Improving Hospitals
This rare good news documentary reports on a surprising solution to escalating costs, unnecessary deaths and waste in America’s hospitals. Doctors and nurses tell how they did their best, working overtime, while hospital conditions worsened. They were delighted to learn a new way to improve patient care dramatically and reduce unnecessary deaths, suffering, errors, infections and costs without additional resources or government regulations. continue reading: PBS Documentary: Improving Hospitals - Lean, Mean, Six Sigma Machines
What management claims as the reason for results is not necessarily actually the reason (and this is true not just if they say forced ranking is good [which I disagree with] or lean thinking is good [which I agree with]).
A great difficulty in evaluating management concepts is that the complexity (including interaction) makes it very difficult to determine the results of specific management decisions (separating out the effects of one or several decisions from the hundreds that were made and outside influences, etc.). How much of the success of Google is due to the 20% “engineer time.”Can you calculate the return? I don’t think so. But you can make a judgment that it is a benefit. continue reading: Lean, Mean, Six Sigma Machines - Lean Beyond the Factory Floor
Experts (in TQM, Deming’s idea’s, Six Sigma, BPR, Lean…) always stress the importance of involving not just others (when talking to management) but their (managers) work too. But fairly consistently management adopts improvement ideas mostly for others, not for their own work. As organizations apply management improvement ideas on some portion of the work the talk of going beyond “factory floor” improvements becomes more common as improvements are seen where it is applied.
Fast Cycle Change in Knowledge-Based Organizations by Ian Hau and Ford Calhoun, Jun 1997 is a good example of lean thinking, eliminating waste… outside the factory floor. continue reading: Lean Beyond the Factory Floor - Toyota IT for Kaizen
IT often does the opposite of lean management and makes things more complex, more prone to error, less effective, etc.. Often all in search of only one thing – cutting costs. For that people should not be faulted for being skeptical of IT solutions. However, that does not mean that IT cannot play a part in improvements. It can, just be careful.
I find it a good sign when the CIO office is helping people find solutions at the request of the users rather than dictating solutions from on high. Some of the dictating might be necessary to optimize the system of IT (some local sub optimization may be required for the overall good) but in my opinion this is used as an excuse far too often.
Related: The Edge-case Excuse (a post I wrote more recently on the topic of error prone IT solutions) continue reading: Toyota IT for Kaizen - Trust: Respect for People
Management then vowed that this (layoffs in 1950) would be the first and last time such an event would come to pass at Toyota, and, in a gesture of respect to former employees, Kiichiro resigned from his position as president of the company.
A bit different than laying off tens of thousands of workers and then taking huge bonuses [the broken link was removed]. And in case you don’t know, I think Toyota’s approach is more honorable and what should be aimed for (I wouldn’t say the president always should resign but it should be a significant admission of failure).
Does this mean no workers ever come into conflict with Toyota management? No. But Toyota’s respect for workers is qualitatively different than that of most companies.
Related: Bad Management Results in Layoffs continue reading: Trust: Respect for People - CEO Flight Attendant
This getting out and seeing work in action is exposed a great deal, including a lean management concept, Genchi Genbutsu – to go to see the problem in situ (not just reading a report about it).
The success of many management practices is more a matter of how the practice is done than if it is done. Also the success depends on the rest of the management system. Practices cannot just be copied. But you can learn from what others find useful and figure out how that idea would work within your organization. continue reading: CEO Flight Attendant
|