Blog posts on lean manufacturingPosts selected fromManagement Blog - Engineering Blog - Investing Blog and other blogs - Early "Lean" Thinking
Here are some early reports (so early it preceded the lean terms widespread use). It also means the focus hasn't already been set by the Machine that Changed the World but it is the same stuff that those that studied in 1980, 1990, 2000 or 2013 saw - it is more about respect for people and using everyone's brain than any specific tool. And these articles have a bit more focus on using statistics and data than much of lean literature today (partially because George Box and Dad were statisticians and partially, in my opinion, because current lean literature is light on using data). continue reading: Early "Lean" Thinking - Toyota as Homebuilder
many organizations don’t apply many concepts that have been proven effective for decades. So I hope Toyota gets into any business that continues to provide lousy value to the consumer (at least those where that consumer is me). I wish they would create their own credit card (they offer Toyota branded Visa and MasterCard credit cards now, in Japan), provide high speed internet service and run an airline.
Toyota is probably too smart to try and run an airline in the US (only Southwest seems to be able to that profitably).
...
On the Toyota web site they list the following areas of non-automotive Toyota business: financial services, information and communications, marine and most surprisingly Biotechnology and Afforestation. Toyota states: “Biotechnology may seem far removed from the auto industry. It is, however, closely related to automaking in the context that they are both aiming to achieve a sustainable society, and their close relationship can be seen in the new Raum, launched in May 2003, which uses parts made from bioplastics.” continue reading: Toyota as Homebuilder - New Toyota CEO’s Views (2005)
Toyota has grown in the past few years, but [there’s a risk] that a belief that the current status is satisfactory creeps into the minds of employees. That’s what I’m worried about.
We should never be satisfied with the current status. In each division, function, or region, we still have numerous problems to cope with. We need to identify each one of those tasks or problems and fully recognize them and pursue the causes. This needs to be done by all the people working for Toyota.
continue reading: New Toyota CEO’s Views (2005) - How Toyota Turns Workers Into Problem Solvers
This idea is simple. Creating an environment where this is actual the way things are, not just the way things are said to be, is difficult. That is why I believe so strongly in Deming’s management philosophy. The organization must be viewed as a whole. Benefits can be gained by adopting some concepts in a piecemeal manner. However, many benefits accrue only when the positive interactions between Toyota Production System (TPS – Lean) concepts occur (as systems thinking would predict). continue reading: How Toyota Turns Workers Into Problem Solvers - There is Much to Improve in How We Use the Internet to Serve Customers
Webinars can have great interaction. They can provide very useful archived webinars covering some content (live webinars could be provided for free too if the reward was worth the cost) . If the public finds that free content valuable it can be about the most effective marketing in many ways including for gaining customers for live interactive webinars on more advanced topics.
Webinars also allow the presenter to do multiple two hour sessions for different clients anywhere in the world in the same day. So you could customize your content to specific client needs. Also each of those sessions could include employees from multiple sites around the globe. continue reading: There is Much to Improve in How We Use the Internet to Serve Customers - Toyota Engineers a New Plant: the Living Kind
Toyota’s vision:
First, making things that benefit both people and the world as a whole. … Second, as a member of society, we must fulfill our responsibilities to all stakeholders. We must provide to customers cleaner, safer, and more attractive products with excellent value. To shareholders, we must enhance share value through long-term and stable growth by increasing profits and paying appropriate dividends. With business partners, we must engage in fair business based on a spirit of mutual benefit.
To our employees, we must provide a workplace where they can work with pride based on mutual trust and responsibility between labor and management, and respect for people.
continue reading: Toyota Engineers a New Plant: the Living Kind - Be Thankful for Lean Thinking
Through better information engineering, supply chain improvements have resulted in a reduced bullwhip effect, lower inventory levels, reduced logistics costs, and streamlined payments. These improvements appear to have helped produce macroeconomic benefits such as more stable economic output and higher productivity growth.
continue reading: Be Thankful for Lean Thinking - Interview with Jim Womack (2005)
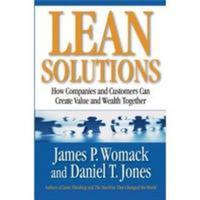
The whole idea of lean solutions is to start with today’s customer in today’s circumstances and ask what the customer really wants. When we do this, the first thing to note is that manufactured goods have gotten vastly better, somewhat cheaper
...
But we have also noticed for years the growing gap between the factory, where things are getting better, and the situation of providers and consumers where it often appears that things are getting worse.
continue reading: Interview with Jim Womack (2005) - Management Improvement Flavors
Some tools are much more common in one program, even if they are not limited to one program (such as Design of Experiments used heavily in six sigma). But design of experiments existed long before six sigma and was used by sensible people to improve for decades before six sigma.
The biggest difference I see in the programs is the overall aim. And that overall aim affects everything else. I happen to be a fan of Deming’s ideas. Most of these programs take a great deal from Deming’s ideas. I believe Lean is closest to Deming’s ideas (which makes sense as Lean is essentially the Toyota Production System TPS). continue reading: Management Improvement Flavors - Toyota Special Report: Thinking Production System
Minoura warns “simply introducing kanban cards or andon boards doesn’t mean you’ve implemented the Toyota Production System, for they remain nothing more than mere tools. The new information technologies are no exception, and they should also be applied and implemented as tools.”
Early in his career, Minoura worked under Taiichi Ohno, recognized as the creator of the Toyota Production System. Ohno, through tireless trial and error, managed to put into practice a “pull” system that stopped the factory producing unnecessary items. But Minoura observes that it was only by developing this “loose collection of techniques” into a fully-fledged system, dubbed the Toyota Production System or TPS, that they were able to deploy this throughout the company continue reading: Toyota Special Report: Thinking Production System - Is Made in the USA Back In Vogue? (2006)
This example provides more evidence of the benefits of "lean manufacturing," though it seems they are getting only a few benefits (reduction of waste, faster resupply of "hot items") and they may well not know about <a href="http://curiouscat.com/management/leanthinking.cfm">lean thinking</a>. By studying and applying lean ideas they should be able to reduce the 45 day turn-around time. Perhaps they should read the Fashion Incubator blog... continue reading: Is Made in the USA Back In Vogue? (2006) - Deming and Toyota
I believe Toyota applied Deming’s ideas to create a management system and continued to develop that system to create the Toyota Production System (also known as lean manufacturing). continue reading: Deming and Toyota - Lean Manufacturing Success
Not only is this a nice story but it is one small example of the good people working at GM and Ford. The problem is not the individual workers it is management. It is too bad that those companies, that did take great strides in the 1980 and early 1990s to improve (starting with Deming’s Management ideas) let those efforts fade away. continue reading: Lean Manufacturing Success - Trust: Respect for People
Management then vowed that this (layoffs in 1950) would be the first and last time such an event would come to pass at Toyota, and, in a gesture of respect to former employees, Kiichiro resigned from his position as president of the company.
A bit different than laying off tens of thousands of workers and then taking huge bonuses [the broken link was removed]. And in case you don’t know, I think Toyota’s approach is more honorable and what should be aimed for (I wouldn’t say the president always should resign but it should be a significant admission of failure).
Does this mean no workers ever come into conflict with Toyota management? No. But Toyota’s respect for workers is qualitatively different than that of most companies.
Related: Bad Management Results in Layoffs continue reading: Trust: Respect for People - TQM for the Water Business
Deming did not like the term TQM. It was not defined, so each person using it meant something different. And the faddish nature of the term drew a large number of “hacks” (consultants who spoke with authority but without knowledge). Seeing the term TQM used now [2006] however, I find refreshing. To use the term TQM you must go against the temptation to talk only about the current fad (learning organizations, reengineering, balanced scorecard, six sigma, lean…). This author defines what he means by TQM... continue reading: TQM for the Water Business
|