Posts selected fromManagement Blog - Engineering Blog - Investing Blog and other blogs - What is a Lean Program, Deming Program?
Lean has evolved away, IMO, from just being able to say anything Toyota does is by definition lean. Lean and Deming are more about a philosophy of managing - continual improvement, respect for people, etc. than prescriptions. So you can't really have a checklist and say that if your org can check off all these things they are lean or Deming. The fact that the management systems can't be reduced to a checklist is a necessary given the long lasting power they offer. continue reading: What is a Lean Program, Deming Program? - Toyota as Homebuilder
many organizations don’t apply many concepts that have been proven effective for decades. So I hope Toyota gets into any business that continues to provide lousy value to the consumer (at least those where that consumer is me). I wish they would create their own credit card (they offer Toyota branded Visa and MasterCard credit cards now, in Japan), provide high speed internet service and run an airline.
Toyota is probably too smart to try and run an airline in the US (only Southwest seems to be able to that profitably).
...
On the Toyota web site they list the following areas of non-automotive Toyota business: financial services, information and communications, marine and most surprisingly Biotechnology and Afforestation. Toyota states: “Biotechnology may seem far removed from the auto industry. It is, however, closely related to automaking in the context that they are both aiming to achieve a sustainable society, and their close relationship can be seen in the new Raum, launched in May 2003, which uses parts made from bioplastics.” continue reading: Toyota as Homebuilder - Could Toyota Fix GM
Yes, Toyota could fix GM. Even the right leaders and managers, within GM, could fix GM but it is a huge long term job and it would be harder to do it internally because you will have to do it while competing with Toyota. Also they have some difficult issues to deal with since their previous managers did not tihnk of the long term (20-50 years out from the decisions they were making in the 70s though 90s).
I wouldn’t buy GM if I were Toyota, though. Why bother. Just grow Toyota, it is working very well so far. It makes sense to buy if you need to grow quickly to gain critical mass, or you will lose the opportunity to grow early in a fast moving market. High tech companies (like Cisco and Intel) often do well buying other companies – but just as often high tech companies make more mistakes buying than is justified by the successes. continue reading: Could Toyota Fix GM - New Toyota CEO’s Views (2005)
Toyota has grown in the past few years, but [there’s a risk] that a belief that the current status is satisfactory creeps into the minds of employees. That’s what I’m worried about.
We should never be satisfied with the current status. In each division, function, or region, we still have numerous problems to cope with. We need to identify each one of those tasks or problems and fully recognize them and pursue the causes. This needs to be done by all the people working for Toyota.
continue reading: New Toyota CEO’s Views (2005) - Jeff Bezos on Lean Thinking (2005)
I read a book recently about Toyota’s lean production methodology, which is very interesting
continue reading: Jeff Bezos on Lean Thinking (2005) - Toyota Engineers a New Plant: the Living Kind
Toyota’s vision:
First, making things that benefit both people and the world as a whole. … Second, as a member of society, we must fulfill our responsibilities to all stakeholders. We must provide to customers cleaner, safer, and more attractive products with excellent value. To shareholders, we must enhance share value through long-term and stable growth by increasing profits and paying appropriate dividends. With business partners, we must engage in fair business based on a spirit of mutual benefit.
To our employees, we must provide a workplace where they can work with pride based on mutual trust and responsibility between labor and management, and respect for people.
continue reading: Toyota Engineers a New Plant: the Living Kind - Toyota Manufacturing Powerhouse
Unusual among automakers, “they don’t hide a lot,” Coventry said. “It’s like going to the Super Bowl and having the opposite side throw their playbook on the table. It’s as if they feel they can still beat you on the field.”
Toyota has greatly advanced management practice worldwide through their actions.
In a reflection of Toyota’s team-oriented approach, its executive pay is paltry by U.S. standards. Analyst Ron Tadross at Banc of America Securities estimates the total annual compensation of Toyota’s CEO at under $1 million – about as much as a vice president at GM or Ford Motor Co. makes in a good year.
The executive pay crisis in America is a symptom of the failure of American management to understand their role. Executives are part of the system and have acted shamefully in allowing obscene pay for a few while claiming they must force others to suffer (due to “the market”). continue reading: Toyota Manufacturing Powerhouse - Poor Management Harms USA Manufactures (2005)
The global competition in manufacturing is intense. But America is still the largest manufacturer in the world and managers should not be allowed escape responsibility for their failure to manage effectively with claims that manufacturing in the USA cannot compete. The biggest change needed is an improvement in management. Other things would also help greatly, such as improving the health care system. continue reading: Poor Management Harms USA Manufactures (2005) - Toyota Special Report: Thinking Production System
Minoura warns “simply introducing kanban cards or andon boards doesn’t mean you’ve implemented the Toyota Production System, for they remain nothing more than mere tools. The new information technologies are no exception, and they should also be applied and implemented as tools.”
Early in his career, Minoura worked under Taiichi Ohno, recognized as the creator of the Toyota Production System. Ohno, through tireless trial and error, managed to put into practice a “pull” system that stopped the factory producing unnecessary items. But Minoura observes that it was only by developing this “loose collection of techniques” into a fully-fledged system, dubbed the Toyota Production System or TPS, that they were able to deploy this throughout the company continue reading: Toyota Special Report: Thinking Production System - Innovation at Toyota in Developing the Prius
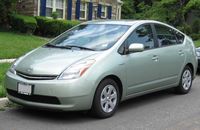
By the end of 1993 the development team had determined that higher oil prices and a growing middle class around the world would require the new car to be both roomy and fuel-efficient. Other than that, they were given no guidance. “I was trying to come up with the future direction of the company,” says Watanabe, who headed corporate planning at the time. “I didn’t have a very specific idea about the vehicle.”
Investing in innovation is risky. If successful, the benefits can build a competitive advantage that is difficult for others to eliminate. However, others will try and if you fail to execute as well in the future those benefits can disappear quickly. Toyota shows few signs of letting others catch up though.
continue reading: Innovation at Toyota in Developing the Prius - Deming and Toyota
I believe Toyota applied Deming’s ideas to create a management system and continued to develop that system to create the Toyota Production System (also known as lean manufacturing). continue reading: Deming and Toyota - People: Team Members or Costs
Both Toyota and GM seek to use technology to improve but Toyota sees the technology as useful to help people to be more efficient, eliminate menial repetitive tasks, eliminate tasks that cause injury… and it seems to me GM saw technology as a way to eliminate people. The action showed a company that viewed people as a cost to be eliminated. GM did not act as though people were their “most important assets” as we so often hear, but see so little evidence of in the action of companies.
Toyota does try to reduce overall costs (including labor costs) by continually improving and making cars more and more efficiently (so they can produce cars using fewer hours of labor in the future than they need today). Trying to become more efficient by engaging everyone in the effort is a part of the system of management at Toyota. The current Toyota employees are an important part of the system and are not viewed as a cost to eliminate.
continue reading: People: Team Members or Costs - A Company’s Purpose is to be Useful to Society
- Toyota in the US Economy
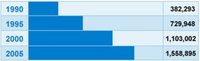 From Toyota’s web site: Toyota Manufacturing in the USA: by 2008, Toyota will have the annual capacity to build 1.81 million cars and trucks, 1.44 million engines, and 600,000 automatic transmissions in North America.
The company’s direct employment in North America is more than 38,000 and direct investment is nearly $16.8 billion with annual purchasing of parts, materials, goods and services from North American suppliers totaling an additional $26 billion.
[In 2016 Toyota manufactured 2,450,000 vehicles in the USA, Toyota promotes a fake number for employees counting many non-employees, employees of suppliers etc., so you can't view the accurate data on their site in 2017 - in 2006 they did post an honest number]. continue reading: Toyota in the US Economy - Toyota IT for Kaizen
IT often does the opposite of lean management and makes things more complex, more prone to error, less effective, etc.. Often all in search of only one thing – cutting costs. For that people should not be faulted for being skeptical of IT solutions. However, that does not mean that IT cannot play a part in improvements. It can, just be careful.
I find it a good sign when the CIO office is helping people find solutions at the request of the users rather than dictating solutions from on high. Some of the dictating might be necessary to optimize the system of IT (some local sub optimization may be required for the overall good) but in my opinion this is used as an excuse far too often.
Related: The Edge-case Excuse (a post I wrote more recently on the topic of error prone IT solutions) continue reading: Toyota IT for Kaizen
|