Posts selected fromManagement Blog - Engineering Blog - Investing Blog and other blogs - Competition
Most aspects of Deming’s thinking seemed natural to me from the start. Some ideas have taken longer (it took me awhile to be won over to the harm caused by performance appraisals, for example). Competition is another area that I still struggle with. I have been moved greatly by my experience and the thoughts of people like Alfie Kohn (No Contest: The Case Against Competition).
But I still hold more promise for some aspects of competition and I hold less concern than some about other aspects of competition. Still I agree that there is a good deal to learn about the dangers of competition which often creates havoc within a system. continue reading: Competition - Dangers of Extrinsic Motivation
Joel Spolsky notes that relying on extrinsic motivation to drive performance is an abdication of management.
Instead of training developers on techniques of writing reliable code, you just absolve yourself of responsibility by paying them if they do. Now every developer has to figure it out on their own.
continue reading: Dangers of Extrinsic Motivation - Interviews with Innovators
The very first thought in my mind was, “I think I signed a document that everything I design belongs to Hewlett-Packard.” Even just on my own time, I thought that they deserved it first. And I wanted Hewlett-Packard to build this. I loved my division. I was going to work there for life. It was the calculator division; it was the right division to move into this kind of a computer.
I went to management, and I had three levels of bosses above me in a room and a couple of other engineers, and I presented the ideas and told them what we could do at what price and how it would work. They were intrigued by it, but they couldn’t justify it as a Hewlett-Packard product for some good reasons. Hewlett-Packard couldn’t do a simple project, which was really what was interesting.
Steve Wozniak, on what became Apple. continue reading: Interviews with Innovators - Vacation: A Systems Thinking Perspective
Health care insurance costs are high, if you can get 1900 hours of work a year for the health care premium instead of 1500 hours that can add up to a great deal of savings... continue reading: Vacation: A Systems Thinking Perspective - What Is Muda?
And the biggest waste of all is the underutilization of people’s talents. If you just learn to ask people for their ideas and get them to participate in creative problem-solving activities, you will be amazed at what people can do.
Norman Bodek
I agree: "Two resources, largely untapped in American organizations, are potential information and employee creativity. Managing Our Way to Economic Success, William G. Hunter, 1987. Also "The greatest waste in America is failure to use the ability of people." W. Edwards Deming, Out of the Crisis, 1982. continue reading: What Is Muda? - Another Quota Failure Example
However, as I was to learn from Dr Deming, this was judging performance using arbitrary goals, which fostered short-term thinking – the only thing they cared about was: Did I make my quota this week? Misguided focus. The focus was not at all on the customer. The focus was: How much money can I make off this customer? … It created a lot of internal conflict. What type of internal conflict? Well, the salespeople hated having new salespeople hired on the floor, because they felt like it would cut into their commission…
Also, judging performance using arbitrary goals fostered a giant amount of fudging of the figures.
Jim McIngvale, CEO Gallery Furniture and author of Always Think Big. continue reading: Another Quota Failure Example - Motivation is Most Often Misguided
- Shaker Village of Pleasant Hill, Kentucky
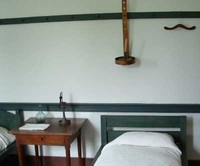 - IT Outsourcing to India Slowing (2006)
Outsourcing IT makes a lot of sense but it is complex to do well. The first rush of outsourcing was just an attempt to save money by moving work to sites where the workers could be paid less. This is classic economics and the economic theory has worked well. Capitalists moved work to where the competitive advantage was. The economic reaction was what you would expect – Indian IT wages raised drastically and other costs of doing business have continued to rise (much higher turnover as the opportunities that workers had expanded they jump from one job to another). continue reading: IT Outsourcing to India Slowing (2006) - The Future for Investors
The subtitle captures the basic theme of the book. Investing in the boring old stocks that people are not excited about is what have performed best.
His basic advise is still to buy the broadest market index fund (such as the Vanguard Total Stock Market Index Fund [the broken link was removed]). He also concludes with the advice that those returns have been beaten historically by focusing on stocks with high dividend yields and low price earnings ratios. continue reading: The Future for Investors - Usability Failures
I guess if you operationally define “nothing wrong” as a failure to work as the manufacturer intended that would be true. But is that what really matters? What is the number of defects that should be counted?
The design of the phone is broken if 63% of the returns work as intended and customers still think they are broken. You might argue that the instructions are bad, but really shouldn’t people just be able to use the phone if it is designed well? continue reading: Usability Failures - New Rules for Management? No!
“New” rule: “The customer is king.” Yes. GE would have said the same thing. Shareholders rule as the old rule? Yeah they still seem to. Few companies today, 10 years ago, 50 years ago… understand that there are many stakeholders – all of which the organization should benefit: customers, stock holders, suppliers, workers, the community… I see no evidence there has been any shift in thinking.
“New” rule: “Look out, not in.” What kind of rule is that? It is pretty obvious you need to do both. I find it incredible the amount of time that is taken trying to show “new” ideas that amount to absolutely nothing. See comments on: Fast Company Interview: Jeff Immelt. continue reading: New Rules for Management? No! - The Exciting Life of Industrial Statisticians
All of this provides great new opportunities for industrial statisticians to serve as statistical leaders-a term popularized by the late and great Ed Deming (see Hahn and Hoerl, 1998). Statistical leaders engage principally in leveraging statistical concepts and thinking (see Hoerl, Hooper, Jacobs and Lucas , 1993), and focus their activities on mentoring and supporting the most business-vital and technically challenging problems dealing with getting the right data, and converting such data into actionable information.
continue reading: The Exciting Life of Industrial Statisticians - Reducing Waste - Zero Waste to Landfill
A great improvement strategy. Determine what you are trying to do. Understand the system. Set up process measures that measure that system. Improve the system and track the results. Repeat. Maintain focus over the long term. Result: success. continue reading: Reducing Waste - Zero Waste to Landfill - Supplier Development Article
|