Blog posts on continual improvementPosts selected fromManagement Blog - Engineering Blog - Investing Blog and other blogs - Management Improvement History
I do believe we need to improve our practice of Quality (and to do that we need to understand what happened in the past and why it was not more successful). The idea that Design of Experiments (DoE) was at the core of some Quality Movement to me is not at all accurate.
In my experience only a few Quality professionals today understand what it means and how it should be applied. The idea that it was common place in the 40’s I seriously doubt (though I don’t have first hand knowledge of this). I find it difficult to believe we would have decided to stop using DoE if it was commonly done previously. The understanding I have from those that should know (like George Box and previously my father – Bill Hunter) is that it was not at all common practice and still is not outside of a few industries and even there it is isolated in the domain of a few experts.I do have first hand knowledge of the 80’s and the idea that we did “employee training in problem solving, team activities and just-in-time inventory” well is not even close to accurate. We sent people to training on these things but other than JIT inventory the effectiveness of these efforts were poor (with a few exceptions that really did well).
“Quality” is not being practiced anywhere close to the level with which I am satisfied with in more than a few organizations. We have huge improvements to make in the practice of DoE, SPC, process improvement, having decisions made by the appropriate level (as close to the issue as possible), leadership, teamwork, data based decision making, the use of basically all the Quality tools, systems thinking, transformation… continue reading: Management Improvement History - Operational Excellence
Saying the organization is focuses on new principles (partnering, lean, etc.) is not the same as applying those principles with the great success that Toyota does. That difference is huge and is driving many companies to outsource and try to dramatically cut costs. Reducing costs should be the outcome of improving efficiency.
Toyota is successful manufacturing in the USA.
...
I would agree that many companies don’t understand the critical importance of management excellence. Rather than take the difficult path to lead real change in their organization they focus on simple cost cutting measures (though usually not cutting executive salaries which have grown dramatically and are excessive in the USA compared to the rest of the world). That won’t work. continue reading: Operational Excellence - Control Charts in Health Care
The point of using a control chart, and many of the management improvement tools, are to improve the efficiency and effectiveness of resources spent improving. The trick is not really to improve (that is pretty easy) the trick is to improve quickly and effectively (and in a competitive marketplace to improve more quickly than competitors). Where improvement resources are targeted is critical. In deciding which improvement options to explore it is important to understand the impact on the outcome (in this case the health of the patient). continue reading: Control Charts in Health Care - Lean Management in Policing
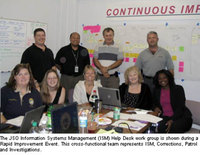
Hiring of school crossing guards made more expedient. “This one’s amazing,” Sheriff Rutherford chuckles. “It was taking us 68 days to hire someone from our eligibility list because we were sending candidates all over for different parts of the interview process. Now it takes us just three days to make a decision because we’re practicing ‘one-stop hiring.'”
continue reading: Lean Management in Policing - Management is Prediction
I believe Deming’s thoughts about prediction are most effectively put into action using the PDSA cycle. Specifically, you must predict the results in the planning phase (prior to piloting improvements). I find that this is rarely done. I don’t think the form of that prediction is critical (narrative with loose numerical guesses, precise numerical prediction…). The critical issue is making the prediction, then comparing the results to that prediction and then figuring out how your original understanding can be improved based on the new data.
Learning will not only be about the specific case being examined, but also, over time, learning about your tendencies in prediction. continue reading: Management is Prediction - Lean Government
I was one of the founding board members on the ASQ Public Sector Network (now the ASQ Government Division). I also, created and have maintained the Public Sector Continuous Improvement web site for a decade (some additional details on my background).
There have been many great efforts in the government, but still so much more needs to be done.
Here are articles exploring what has been done:
continue reading: Lean Government - Box on Quality
 Dr. George Box is not as well known in the general management community as his ideas merit (in my biased opinion – photo of Bill Hunter and George Box). He is well know in the statistics field as one of the leading statistical minds. Box on Quality is an excellent book that gathers his essays from his 65th to 80th year. continue reading: Box on Quality - Management Improvement Flavors
Some tools are much more common in one program, even if they are not limited to one program (such as Design of Experiments used heavily in six sigma). But design of experiments existed long before six sigma and was used by sensible people to improve for decades before six sigma.
The biggest difference I see in the programs is the overall aim. And that overall aim affects everything else. I happen to be a fan of Deming’s ideas. Most of these programs take a great deal from Deming’s ideas. I believe Lean is closest to Deming’s ideas (which makes sense as Lean is essentially the Toyota Production System TPS). continue reading: Management Improvement Flavors - Fear Remains a Toyota Motivator
First, don’t let the title fool you, this is not an indication Toyota is going against Deming’s obligation of management to “Drive out fear and build trust so that everyone can work effectively”.
...
Rather than being drawn to improve it is most often stated as being scared that if we don’t we will have to pay for failing to improve. Thus the reference to fear. continue reading: Fear Remains a Toyota Motivator - Innovate or "Play it Safe: to Avoid Risk
There are many reasons why avoiding risks is smart and should be encouraged. But when avoiding risks stifles innovation the risks to the organization are huge.
Playing it safe isn't always safe. In rapidly changing markets (which are quite common lately) "playing it safe" is often riskier than "taking chances" on new ideas. continue reading: Innovate or "Play it Safe: to Avoid Risk - Toyota's Planet Kaizen
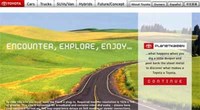 It requires flash to view Planet Kaizen. I think it has amazingly bad visual controls (as do many flash applications). I can’t figure out why it would be done in flash – other than some marketing person, or IT person, thought it would be cool. I certainly don’t see how kaizen practices could have produced such an application. It seems to me one of the examples of how far Toyota still has to go. Of course, as an automobile manufacturer failing to develop web applications well, is better than failing at manufacturing cars well. continue reading: Toyota's Planet Kaizen - Public Sector Management Using Deming's Ideas
Madison’s quality improvement efforts began after then-Mayor James F. Sensenbrenner and his staff were exposed to the teaching of W. Edwards Deming in 1983. A pilot project at the motor equipment division made substantial improvements in prioritizing repairs, improving communications with customers, reducing steps in the inventory purchasing process and, ultimately, reducing vehicle down time, all of which saved money and improved service at the same time. Based on the success of the pilot, it was decided to expand the philosophy throughout city government.
continue reading: Public Sector Management Using Deming's Ideas - Zero Defects
I do not believe you succeed by declaring your goal to be zero defects. You succeed by creating a culture of never ending improvement, of customer focus, of fact based decision making, of learning, of “empowerment”…
Part of that improvement is reducing variation, reducing defects, implementing smart new mistake proofing but innovation is too. Effectively zero defects is not really achievable in most cases. Defects are largely a matter of definition. As performance improves expectations will often rise. When you eliminate anything you would have called a defect years ago, standards are higher and things that would not have been called defects are no longer acceptable. At some point the system process advances to such a level where zero defects is possible in some cases but in many (say medical care, air transportation, education, computer software, restaurants, government, management consulting, civil engineering, legal services…) I really think it is basically impossible. continue reading: Zero Defects - Change is not Improvement
We trained hard… but it seemed that every time we were beginning to form up into teams we would be reorganized. I was to learn later in life that we tend to meet any new situation by reorganizing; and a wonderful method it can be for creating the illusion of progress while producing confusion; inefficiency, and demoralization.
These lines, from the Satyricon of Petronius written 2,000 years ago…*
* Unfortunately it seems this quote is not actually his. continue reading: Change is not Improvement - Learning, Systems and Improvement
Errors of omission, lost opportunities, are generally more critical than errors of commission. Organizations fail or decline more frequently because of what they did not do than because of what they did.
...
The corrective action is itself the result of a decision. A record of this decision should be made and treated as the original decision. In this way the process can not only yield learning but also learning how to learn.
A record of the entire process (all four steps) should be made and stored for easy access by those who may later be confronted by the need to make a similar type of decision.
Russel Ackoff continue reading: Learning, Systems and Improvement
|