Blog posts on continual improvementPosts selected fromManagement Blog - Engineering Blog - Investing Blog and other blogs - People: Team Members or Costs
Both Toyota and GM seek to use technology to improve but Toyota sees the technology as useful to help people to be more efficient, eliminate menial repetitive tasks, eliminate tasks that cause injury… and it seems to me GM saw technology as a way to eliminate people. The action showed a company that viewed people as a cost to be eliminated. GM did not act as though people were their “most important assets” as we so often hear, but see so little evidence of in the action of companies.
Toyota does try to reduce overall costs (including labor costs) by continually improving and making cars more and more efficiently (so they can produce cars using fewer hours of labor in the future than they need today). Trying to become more efficient by engaging everyone in the effort is a part of the system of management at Toyota. The current Toyota employees are an important part of the system and are not viewed as a cost to eliminate.
continue reading: People: Team Members or Costs - Find the Root Cause Instead of the Person to Blame
Why did they make that error? Why did the process let them make that error? When you follow the why chain a couple more steps you can find root causes that will allow you to find a much more effective solution. You can then pilot (PDSA) an improvement strategy that doesn’t just amount to “Do a better job Joe” or “that is it Joe we are replacing you with Mary.” Neither of those strategies turns out to be very effective.
But investigating a bit more to find a root cause can result in finding solutions that improve the performance of all the workers. continue reading: Find the Root Cause Instead of the Person to Blame - Managing with Control Charts
...if managers mistakenly tamper with a stable process, believing an occurrence is exceptional, they introduce an external cause, which destabilises it. Targets do the same thing. continue reading: Managing with Control Charts - Better and Different
The answer, as I see it, is to be better and different (when necessary).
...
if you have to choose one, just being better will work most of the time. The problem is (using an example from Deming, page 9 New Economics) when, for example, carburetors are eliminated by innovation (fuel injectors) no matter how well you make them you are out of business.
Often people mistake Deming’s ideas as only about being better. He stressed not only continual improvement (Kaizen, incremental improvement, SPC) but also innovation. He stressed innovation both in the normal sense of innovating new products for customers and also innovation in managing the organization. continue reading: Better and Different - George Box Webcast on Statistical Design in Quality Improvement
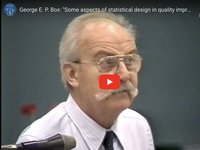 There is great value in creating iterative processes with fast feedback to those attempting to design and improve. Box and Deming (with rapid turns of the PDSA cycle) and others promoted this 20, 30 and 40 years ago and now we get the same ideas tweaked for startups. The lean startup stuff is as closely related to Box’s ideas of experimentation as an iterative process as it is to anything else. continue reading: George Box Webcast on Statistical Design in Quality Improvement - CEO Flight Attendant
This getting out and seeing work in action is exposed a great deal, including a lean management concept, Genchi Genbutsu – to go to see the problem in situ (not just reading a report about it).
The success of many management practices is more a matter of how the practice is done than if it is done. Also the success depends on the rest of the management system. Practices cannot just be copied. But you can learn from what others find useful and figure out how that idea would work within your organization. continue reading: CEO Flight Attendant - Learning from Customers
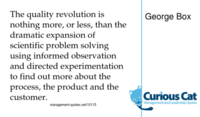 Create a management system focused on continual improvement that is engaged in seeking out customer feedback and continually improving the value provided to customers.
Most organizations do the opposite of this. They make put many barriers in the way of customers speaking to anyone that will listen. They put systems in place to discourage feedback from customers.
... continue reading: Learning from Customers - Quality and Innovation
I really don’t understand how people can talk about innovation as if it were some new discovery. Yes I understand we can bring a different focus to innovation. We can reconfigure management structures to encourage and support innovation. That is good. And new ideas are being developed, but the innovation fad is silly. And accepting the notion that this innovation stuff is some new idea will make managers less effective than if they understand the past.
New Economics by W. Edwards Deming, published in 1992, page 7:
Does the customer invent new product of service? The customer generates nothing. No customer asked for electric lights… No customer asked for photography… No customer asked for an automobile… No customer asked for an integrated circuit.
Innovation has long been important to those interested in management improvement. continue reading: Quality and Innovation - The Exciting Life of Industrial Statisticians
All of this provides great new opportunities for industrial statisticians to serve as statistical leaders-a term popularized by the late and great Ed Deming (see Hahn and Hoerl, 1998). Statistical leaders engage principally in leveraging statistical concepts and thinking (see Hoerl, Hooper, Jacobs and Lucas , 1993), and focus their activities on mentoring and supporting the most business-vital and technically challenging problems dealing with getting the right data, and converting such data into actionable information.
continue reading: The Exciting Life of Industrial Statisticians - Usability Failures
I guess if you operationally define “nothing wrong” as a failure to work as the manufacturer intended that would be true. But is that what really matters? What is the number of defects that should be counted?
The design of the phone is broken if 63% of the returns work as intended and customers still think they are broken. You might argue that the instructions are bad, but really shouldn’t people just be able to use the phone if it is designed well? continue reading: Usability Failures - How Toyota Management Develops a New Camry
- Cease Mass Inspection for Quality
Deming believed in improving the process, and doing so using process measures (which often may involve sampling) to guide improvement efforts. He did not believe in using inspection to select out the bad products, which is what inspection largely was before Deming.
More on Deming’s thought on Inspection... continue reading: Cease Mass Inspection for Quality - Improving the 401(k) System
Many people don’t even take advantage of a 401(k) to save for their retirement. From a public policy perspective it creates a huge long term problem. The economy will end up with millions of people that didn’t save for retirement and will be a drain on those who did save for retirement and the rest of the economy.
So Congress actually passed a good revision to the law. Employers will now be required to default to having employees save for their retirement in 401(k) plans. The employee still has the option to decline doing so, but now, without such a choice, they will automatically save for retirement. continue reading: Improving the 401(k) System - Ackoff, Idealized Design and Bell Labs
“Doesn’t it strike you as odd,” he said, “that the three most important contributions this laboratory has ever made to telephonic communications were made before any of you were born? What have you been doing?” he asked. “I’ll tell you,” he said. “You have been improving the parts of the system taken separately, but you have not significantly improved the system as a whole. The deficiency,” he said, “is not yours but mine. We’ve had the wrong research-and-development strategy. We’ve been focusing on improving parts of the system rather than focusing on the system as a whole. As a result, we have been improving the parts, but not the whole.
We have got to restart by focusing on designing the whole and then designing parts that fit it rather than vice versa.
continue reading: Ackoff, Idealized Design and Bell Labs - Improving on Previous Attempts to Adopt Management Improvement Methods
There is a big difference between needing to improve on previous attempts to adopt management improvement methods and needing to find new methods. Most of what is needed it to actually apply the good ideas that have been around for decades. And yes, sure try and find some new great ideas but where the focus should really be is on the hard work of execution not looking for some magic pill to solve the difficult task of managing well. continue reading: Improving on Previous Attempts to Adopt Management Improvement Methods
|