Posts selected fromManagement Blog - Engineering Blog - Investing Blog and other blogs - Management Improvement Leaders
- Russell Ackoff – frankly I find it difficult to imagine a list management thought leader list, not including his name. Organizational development, systems thinking, management improvement, planning, policy deployment, learning.
- George Box: statistics, design of experiments, finding solutions (problem solving, process improvement), learning, management improvement
continue reading: Management Improvement Leaders - Great Charts
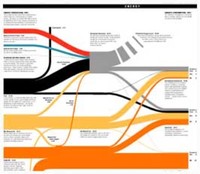 Karl Hartig displays some excellent charts that he created (for the Wall Street Journal) on his web site. The charts seem very similar to what would result from applying Edward Tufte’s ideas. Rarely do I see charts that do such a good job of visually displaying data. The lack of such effective visual display of information is another example of how much improvement could be made just by applying ideas that are already published. continue reading: Great Charts - Zero Defects
I do not believe you succeed by declaring your goal to be zero defects. You succeed by creating a culture of never ending improvement, of customer focus, of fact based decision making, of learning, of “empowerment”…
Part of that improvement is reducing variation, reducing defects, implementing smart new mistake proofing but innovation is too. Effectively zero defects is not really achievable in most cases. Defects are largely a matter of definition. As performance improves expectations will often rise. When you eliminate anything you would have called a defect years ago, standards are higher and things that would not have been called defects are no longer acceptable. At some point the system process advances to such a level where zero defects is possible in some cases but in many (say medical care, air transportation, education, computer software, restaurants, government, management consulting, civil engineering, legal services…) I really think it is basically impossible. continue reading: Zero Defects - Change is not Improvement
We trained hard… but it seemed that every time we were beginning to form up into teams we would be reorganized. I was to learn later in life that we tend to meet any new situation by reorganizing; and a wonderful method it can be for creating the illusion of progress while producing confusion; inefficiency, and demoralization.
These lines, from the Satyricon of Petronius written 2,000 years ago…*
* Unfortunately it seems this quote is not actually his. continue reading: Change is not Improvement - Learning, Systems and Improvement
Errors of omission, lost opportunities, are generally more critical than errors of commission. Organizations fail or decline more frequently because of what they did not do than because of what they did.
...
The corrective action is itself the result of a decision. A record of this decision should be made and treated as the original decision. In this way the process can not only yield learning but also learning how to learn.
A record of the entire process (all four steps) should be made and stored for easy access by those who may later be confronted by the need to make a similar type of decision.
Russel Ackoff continue reading: Learning, Systems and Improvement - Organization, Systems and Culture
Management improvement is mainly about using great ideas that have been around for years and decades.
Useful, innovative new management ideas are great. But far too much effort is placed in trying to package "systems" (or copyrighted terms) as some new breakthrough in management when most often they offer little of value. continue reading: Organization, Systems and Culture - Toyota Special Report: Thinking Production System
Minoura warns “simply introducing kanban cards or andon boards doesn’t mean you’ve implemented the Toyota Production System, for they remain nothing more than mere tools. The new information technologies are no exception, and they should also be applied and implemented as tools.”
Early in his career, Minoura worked under Taiichi Ohno, recognized as the creator of the Toyota Production System. Ohno, through tireless trial and error, managed to put into practice a “pull” system that stopped the factory producing unnecessary items. But Minoura observes that it was only by developing this “loose collection of techniques” into a fully-fledged system, dubbed the Toyota Production System or TPS, that they were able to deploy this throughout the company continue reading: Toyota Special Report: Thinking Production System - Is Made in the USA Back In Vogue? (2006)
This example provides more evidence of the benefits of "lean manufacturing," though it seems they are getting only a few benefits (reduction of waste, faster resupply of "hot items") and they may well not know about <a href="http://curiouscat.com/management/leanthinking.cfm">lean thinking</a>. By studying and applying lean ideas they should be able to reduce the 45 day turn-around time. Perhaps they should read the Fashion Incubator blog... continue reading: Is Made in the USA Back In Vogue? (2006) - Secrets of the World’s Best Companies
As Dr. W. Edwards Deming said there is no instant pudding for management (no quick fix). And management requires customization to the organization. You cannot just copy management practices from one place, where they are successful, to another. You can learn from what has been successful and adopt it to your organization if you have knowledge and theory and know how to test (pdsa) the effectiveness of new ideas in your organization.
I don’t find many of the “secrets” mentioned in the article to be the greatest ideas for management (the best ideas I find among the thoughts of Deming, Ackoff, Ohno, Provost, Csikszentmihalyi, Hoerl, etc..
Still, I believe it is good to learn about what others are doing. continue reading: Secrets of the World’s Best Companies - Performance Appraisal Problems
- Visible Data
Take the time to find the important measures and then don’t keep data hidden in some drawer or computer file out of people’s view and therefore out of mind. Post the important data for everyone to see. Review the data as changes are made and see that the changes had the desired result. continue reading: Visible Data - Quality Customer Focus
Customers expectations change over time. Often what was once enough to delight a customer (remote control for a TV) becomes expected. Once a feature is expected the organization gets no credit for providing it they only risk a negative reaction if they fail to provide it. continue reading: Quality Customer Focus - Innovation at Toyota in Developing the Prius
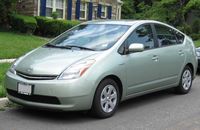
By the end of 1993 the development team had determined that higher oil prices and a growing middle class around the world would require the new car to be both roomy and fuel-efficient. Other than that, they were given no guidance. “I was trying to come up with the future direction of the company,” says Watanabe, who headed corporate planning at the time. “I didn’t have a very specific idea about the vehicle.”
Investing in innovation is risky. If successful, the benefits can build a competitive advantage that is difficult for others to eliminate. However, others will try and if you fail to execute as well in the future those benefits can disappear quickly. Toyota shows few signs of letting others catch up though.
continue reading: Innovation at Toyota in Developing the Prius - Theory in Practice
Knowledge is built upon theory… Rational prediction requires theory and builds knowledge through systematic revision and extention of theory based on comparison of prediction with observation.
W. Edwards Deming, page 102, The New Economics
continue reading: Theory in Practice - Six Sigma Won’t Fix Bad Management?
Like most management concepts how it is applied varies tremendously. If one just uses some tools that are part of the “Six Sigma tool kit” (mostly tools from TQM and the like) then you might improve bad management only marginally.
But if you read the work of Roger Hoerl, Soren Bisgaard, Forrest Breyfogle III… and learn and apply what they talk about as Six Sigma you will definitely have to address bad management practices. Their Six Sigma is definitely a management improvement system (you can’t apply their concepts of Six Sigma without fixing many bad management practices). continue reading: Six Sigma Won’t Fix Bad Management?
|