Blog posts on management systemPosts selected fromManagement Blog - Engineering Blog - Investing Blog and other blogs - Agile Software Development and Deming's Ideas
- Management Improvement History
I do believe we need to improve our practice of Quality (and to do that we need to understand what happened in the past and why it was not more successful). The idea that Design of Experiments (DoE) was at the core of some Quality Movement to me is not at all accurate.
In my experience only a few Quality professionals today understand what it means and how it should be applied. The idea that it was common place in the 40’s I seriously doubt (though I don’t have first hand knowledge of this). I find it difficult to believe we would have decided to stop using DoE if it was commonly done previously. The understanding I have from those that should know (like George Box and previously my father – Bill Hunter) is that it was not at all common practice and still is not outside of a few industries and even there it is isolated in the domain of a few experts.I do have first hand knowledge of the 80’s and the idea that we did “employee training in problem solving, team activities and just-in-time inventory” well is not even close to accurate. We sent people to training on these things but other than JIT inventory the effectiveness of these efforts were poor (with a few exceptions that really did well).
“Quality” is not being practiced anywhere close to the level with which I am satisfied with in more than a few organizations. We have huge improvements to make in the practice of DoE, SPC, process improvement, having decisions made by the appropriate level (as close to the issue as possible), leadership, teamwork, data based decision making, the use of basically all the Quality tools, systems thinking, transformation… continue reading: Management Improvement History - Performance without Appraisal
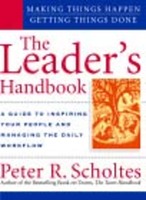 In the short article Performance Without Appraisal: What to do Instead of Performance Appraisals, Peter wrote:
Dr. Deming said of Performance Appraisals, “Stop doing them and things will get better.” He was correct. Many organizations, however, wonder what to do instead.
For those that do require “some alternative” Peter included some good ideas in The Leader’s Handbook(see chapter 9 “Performance without Appraisal pages 293 to 368). This chapter has excellent material for any manager. continue reading: Performance without Appraisal - Targets Distorting the System
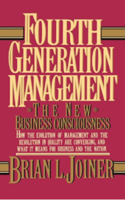 I still remember Dr. Brian Joiner speaking about process improvement and the role of data well over a decade ago. He spoke of 3 ways to improve the figures: distort the data, distort the system and improve the system. Improving the system is the most difficult. continue reading: Targets Distorting the System - Fast Company Interview: Jeff Immelt
My guess would be that what lead to this quote is not a lack of understanding that managers need the same qualities today they needed 10 years ago but the compulsion to feed the media frenzy for some incredible new insight. It just isn’t sexy to say “we need the same leadership qualities we needed in the past.” Deming stressed the importance of these “new” qualities he states more than 50 years ago and I think most decent managers have know you need to “know why we’re doing them”
...
Customer focus and innovation would also be at the top of the list of important issues and were 10 years ago and will be 20 years from now. What is important for management does not change much.
occasionally innovation is so dramatic it drastically changes the practice of management, two examples: 1) the use of information technology 2) the whole quality movement [Deming’s ideas, SPC, Toyota/Lean, Six Sigma… continue reading: Fast Company Interview: Jeff Immelt - Deming’s Ideas at Markey’s Audio Visual
Mark Miller, General Manager, Markey’s Audio Visual spoke on Markey’s experience adopting Deming’s ideas.
- Markey’s needs to anticipate the changing needs of customers and anticipate those needs
- Unknown and unknowable – not really unknown just un-measurable (again taught to all employees)
- Gemba – where the real work gets done (the customer interaction – he stressed time and again that the key to their success was Markey’s employees interaction with customers – Markey’s aims to provide the best customer experience the customer has with any company)
- Break down barriers between departments – Markeys doesn’t charge internally. Indianapolis looses money – they own the high end equipment used by the other offices.
- Intrinsic motivation v. Extrinsic motivation – he has the chart from page 122 of New Economics in Deming’s handwriting on his wall.
continue reading: Deming’s Ideas at Markey’s Audio Visual - Performance Without Appraisal
The comments on the mini-microsoft blog shows performance appraisal continues to be an emotional topic. People on opposite sides of the debate are very passionate.
I admit it took me longer to accept Dr. Deming’s thoughts on performance appraisal than other ideas (and that is even with Peter Scholtes being a friend which gave me the opportunity to discuss the idea with him). So I understand it is not an easy concept to accept. continue reading: Performance Without Appraisal - Statistical Techniques for Quality
As six sigma has taken the business world by storm in the past 15 years, many organizations have focused on acquiring and implementing the DMAIC methodology with performance benchmarks defined by “sigma levels”. However, after perhaps proclaiming the “six sigma organization” label for the company, it is important for the business leaders to look beyond immediate concerns, i.e. those issues embodied in black belt projects, and adopt holistic and forward-looking perspectives in seriously advancing organizational interests.
continue reading: Statistical Techniques for Quality - Lean Government
I was one of the founding board members on the ASQ Public Sector Network (now the ASQ Government Division). I also, created and have maintained the Public Sector Continuous Improvement web site for a decade (some additional details on my background).
There have been many great efforts in the government, but still so much more needs to be done.
Here are articles exploring what has been done:
continue reading: Lean Government - Toyota Engineers a New Plant: the Living Kind
Toyota’s vision:
First, making things that benefit both people and the world as a whole. … Second, as a member of society, we must fulfill our responsibilities to all stakeholders. We must provide to customers cleaner, safer, and more attractive products with excellent value. To shareholders, we must enhance share value through long-term and stable growth by increasing profits and paying appropriate dividends. With business partners, we must engage in fair business based on a spirit of mutual benefit.
To our employees, we must provide a workplace where they can work with pride based on mutual trust and responsibility between labor and management, and respect for people.
continue reading: Toyota Engineers a New Plant: the Living Kind - New Business Ideas Take Time
- Management Improvement Flavors
Some tools are much more common in one program, even if they are not limited to one program (such as Design of Experiments used heavily in six sigma). But design of experiments existed long before six sigma and was used by sensible people to improve for decades before six sigma.
The biggest difference I see in the programs is the overall aim. And that overall aim affects everything else. I happen to be a fan of Deming’s ideas. Most of these programs take a great deal from Deming’s ideas. I believe Lean is closest to Deming’s ideas (which makes sense as Lean is essentially the Toyota Production System TPS). continue reading: Management Improvement Flavors - Toyota Manufacturing Powerhouse
Unusual among automakers, “they don’t hide a lot,” Coventry said. “It’s like going to the Super Bowl and having the opposite side throw their playbook on the table. It’s as if they feel they can still beat you on the field.”
Toyota has greatly advanced management practice worldwide through their actions.
In a reflection of Toyota’s team-oriented approach, its executive pay is paltry by U.S. standards. Analyst Ron Tadross at Banc of America Securities estimates the total annual compensation of Toyota’s CEO at under $1 million – about as much as a vice president at GM or Ford Motor Co. makes in a good year.
The executive pay crisis in America is a symptom of the failure of American management to understand their role. Executives are part of the system and have acted shamefully in allowing obscene pay for a few while claiming they must force others to suffer (due to “the market”). continue reading: Toyota Manufacturing Powerhouse - Google: Ten Golden Rules (2005)
The suits inside Google don’t fare much better than the outside pros. Several current and former insiders say there’s a caste system, in which business types are second-class citizens to Google’s valued code jockeys. They argue that it could prove to be a big challenge in the future as Google seeks to maintain its growth.
Google really is doing things differently. One way you see it is that some of those used to being the most powerful players complain that they don’t get respect at Google, at Google the engineers rule. Um, maybe they shouldn’t complain too loud, maybe the reason Google is doing better is they focus on the Gemba (where value is added to the customer). continue reading: Google: Ten Golden Rules (2005) - Management Excellence
Most management practices cannot be plugged into any organization and work well. That practice must be applied in a sensible way given the organizational system. Learning how lean ideas (or other good ideas) are applied in varying systems can provide insight into how to integrate ideas for organizational improvement from those applying lean practices. continue reading: Management Excellence
|