Blog posts on organization as a systemPosts selected fromManagement Blog - Engineering Blog - Investing Blog and other blogs - Management Training Program
So I said to the Toyota executive, “You’ve only got two or three suppliers per category, and you never take bids. How do you know you aren’t being ripped off?” So this guy, who was around 60, gives me an incredibly frosty look and says, “Because I know everything.” Everything? “That’s my job,” he says.
Reading “Because I know everything” brings to mind an arrogant blowhard to many in America (I think). Probably because most who would say that, are arrogant blowhards. But when someone has worked (a Toyota executive or a baker) for 40+ years in the same area those words can have quite a different meaning than a 31 year old MBA working in his third industry. Managing with constancy of purpose and long term thinking can make a big difference. continue reading: Management Training Program - Management Pioneer Peter Drucker 1909 – 2005
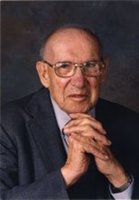
The present people in organizations are still stuck in the 19th-century model of the organization. When big business first emerged throughout the industrial world around 1870, it did not emerge out of the small businesses of 1850 — it emerged independently. The only model available, the most successful organization of the 19th century, was the Prussian Army…
The Prussians succeeded because they had created an organization. They were the first ones to use modern technology effectively, which in those days meant railroad and telegraph. Business copied the command and control structure of the Prussian army, in which rank equaled authority. We are now evolving toward structures in which rank means responsibility but not authority. And in which your job is not to command but to persuade.
continue reading: Management Pioneer Peter Drucker 1909 – 2005 - Managing Innovation
You manage processes such as thinking up a new way to use computer technology differently than you manage a process to manufacture tires. But the idea that you don't manage and improve the process just because the process seems discontinuous is a mistake. continue reading: Managing Innovation - The Economist on Drucker
In the late 1990s he turned into one of America’s leading critics of soaring executive pay, warning that “in the next economic downturn, there will be an outbreak of bitterness and contempt for the super-corporate chieftains who pay themselves millions.”
continue reading: The Economist on Drucker - Superior Customer Experiences Start with Respect for Employees
Oakley found that there is a direct link between employee satisfaction and customer satisfaction, and between customer satisfaction and improved financial performance. Employee satisfaction is a key antecedent to employee engagement. He also found that organizations with engaged employees have customers who use their products more, and increased customer usage leads to higher levels of customer satisfaction.
This is not a zero-sum game. Good managers grow the pie so all the stakeholders can get more benefit (customers, investors, employees…). continue reading: Superior Customer Experiences Start with Respect for Employees - Eliminating Complexity from Work
as much as half of the activities of about sixty people had been to set up and take down jobs, expedite, move material, count material, and do other tasks that were unnecessary in the new process.
Tim Fuller's article discusses how much inneficiency was removed from the process by adopting single piece flow in 1985. How long did it take for management practice to understand this? Certainly this understanding wasn't widespred in 2005. I am not even sure it if it is widely understood and systems have been designed or redesigned with this knowledge in 2017. continue reading: Eliminating Complexity from Work - Toyota Manufacturing Powerhouse
Unusual among automakers, “they don’t hide a lot,” Coventry said. “It’s like going to the Super Bowl and having the opposite side throw their playbook on the table. It’s as if they feel they can still beat you on the field.”
Toyota has greatly advanced management practice worldwide through their actions.
In a reflection of Toyota’s team-oriented approach, its executive pay is paltry by U.S. standards. Analyst Ron Tadross at Banc of America Securities estimates the total annual compensation of Toyota’s CEO at under $1 million – about as much as a vice president at GM or Ford Motor Co. makes in a good year.
The executive pay crisis in America is a symptom of the failure of American management to understand their role. Executives are part of the system and have acted shamefully in allowing obscene pay for a few while claiming they must force others to suffer (due to “the market”). continue reading: Toyota Manufacturing Powerhouse - Excessive Executive Pay
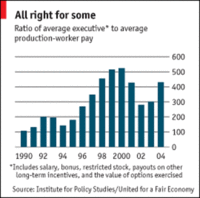 The excesses are so great now they will either force companies to:
- take huge risks to justify such pay and then go bankrupt when such risks fail (and some will succeed making it appear, to some, that the pay was deserved rather than just the random chance of taking a large risk and getting lucky).
- make it impossible to compete with companies that don’t allow such excesses and slowly go out of business to those companies that don’t act so irresponsibly
- hope that competitors adopt your bad practice of excessive pay (this does have potential as most people are corrupted by power, even across cultural boundaries). However, my expectation is the competitive forces of capitalism going forward are going to make such a hope unrealistic. People will see the opportunity provided by such poor management and compete with them.
As long as the pay packages were merely large, and didn’t effect the ability of a company to prosper that could continue (slicing up the benefits between the stakeholders is not an exact science). The excesses recently have become so obscene as to become unsustainable. continue reading: Excessive Executive Pay - Data Based Decision Making at Google and Elsewhere (2005)
Google has done a fantastic job of using data to make decisions. In fact so much so, that some think they may go overboard trying to find an algorithm for everything.
I believe you can’t measure everything that is important. I also believe in most organizations the amount of stuff you can’t measure usefully and realistically is quite a bit higher than it is for Google. Having highly intelligent, skilled and experienced people who can derive complex formulas effectively does greatly expand the effective use of measurements.
Still there are limits, and those limits are much lower for most organizations that have neither, thousands of phd level mathematicians, rocket scientists, software engineers etc. nor a anything approaching Google’s percentage of such people.
Still I think we will benefit from the innovation that will continue to take place at Google. The are making great strides in using data to inform their decision making process. continue reading: Data Based Decision Making at Google and Elsewhere (2005) - Management Excellence
Most management practices cannot be plugged into any organization and work well. That practice must be applied in a sensible way given the organizational system. Learning how lean ideas (or other good ideas) are applied in varying systems can provide insight into how to integrate ideas for organizational improvement from those applying lean practices. continue reading: Management Excellence - The 70 Percent Solution
Google CEO Eric Schmidt:
We spend 70 percent of our time on core search and ads. We spend 20 percent on adjacent businesses, ones related to the core businesses in some interesting way. Examples of that would be Google News, Google Earth, and Google Local. And then 10 percent of our time should be on things that are truly new. An example there would be the Wi-Fi initiative.
continue reading: The 70 Percent Solution - Toyota Special Report: Thinking Production System
Minoura warns “simply introducing kanban cards or andon boards doesn’t mean you’ve implemented the Toyota Production System, for they remain nothing more than mere tools. The new information technologies are no exception, and they should also be applied and implemented as tools.”
Early in his career, Minoura worked under Taiichi Ohno, recognized as the creator of the Toyota Production System. Ohno, through tireless trial and error, managed to put into practice a “pull” system that stopped the factory producing unnecessary items. But Minoura observes that it was only by developing this “loose collection of techniques” into a fully-fledged system, dubbed the Toyota Production System or TPS, that they were able to deploy this throughout the company continue reading: Toyota Special Report: Thinking Production System - Visible Data
Take the time to find the important measures and then don’t keep data hidden in some drawer or computer file out of people’s view and therefore out of mind. Post the important data for everyone to see. Review the data as changes are made and see that the changes had the desired result. continue reading: Visible Data - Airline Quality (or Rather, Lack Thereof)
I flew JetBlue Airways last week. The help at the counter was polite and friendly. While this is only one data point (and hardly a “high bar” to meet) it contrasts with most of my flying experience (in my experience Southwest has a good likelihood of providing good service but few other airlines do). It would be nice if more airlines could be like Southwest... continue reading: Airline Quality (or Rather, Lack Thereof) - Find the Root Cause Instead of the Person to Blame
Why did they make that error? Why did the process let them make that error? When you follow the why chain a couple more steps you can find root causes that will allow you to find a much more effective solution. You can then pilot (PDSA) an improvement strategy that doesn’t just amount to “Do a better job Joe” or “that is it Joe we are replacing you with Mary.” Neither of those strategies turns out to be very effective.
But investigating a bit more to find a root cause can result in finding solutions that improve the performance of all the workers. continue reading: Find the Root Cause Instead of the Person to Blame
|